Discover What is Porosity in Welding and Its Impact on Architectural Honesty
Discover What is Porosity in Welding and Its Impact on Architectural Honesty
Blog Article
Understanding Porosity in Welding: Checking Out Reasons, Effects, and Avoidance Methods
Porosity in welding is a persistent challenge that can considerably affect the high quality and integrity of welds. As specialists in the welding industry are cognizant, recognizing the reasons, impacts, and avoidance strategies connected to porosity is vital for achieving robust and reputable welds. By diving right into the origin triggers of porosity, analyzing its destructive effects on weld high quality, and discovering efficient avoidance methods, welders can improve their understanding and skills to generate high-quality welds constantly. The elaborate interaction of aspects contributing to porosity requires a detailed understanding and a positive strategy to ensure effective welding outcomes.
Common Reasons For Porosity
Contamination, in the kind of dust, oil, or rust on the welding surface, produces gas pockets when heated, leading to porosity in the weld. Incorrect securing happens when the protecting gas, typically used in procedures like MIG and TIG welding, is unable to completely protect the liquified weld pool from reacting with the surrounding air, resulting in gas entrapment and subsequent porosity. Furthermore, inadequate gas coverage, often due to incorrect flow prices or nozzle positioning, can leave components of the weld unsafe, enabling porosity to create.
Results on Weld High Quality
The existence of porosity in a weld can significantly jeopardize the overall top quality and honesty of the welded joint. Porosity within a weld produces spaces or cavities that deteriorate the structure, making it much more susceptible to breaking, rust, and mechanical failing. These gaps act as tension concentrators, reducing the load-bearing ability of the weld and increasing the probability of premature failing under applied anxiety. Furthermore, porosity can likewise act as prospective websites for hydrogen entrapment, more exacerbating the destruction of the weld's mechanical residential or commercial properties.
Additionally, porosity can prevent the effectiveness of non-destructive testing (NDT) strategies, making it testing to spot other defects or gaps within the weld. This can bring about substantial safety concerns, especially in essential applications where the structural honesty of the bonded components is paramount.
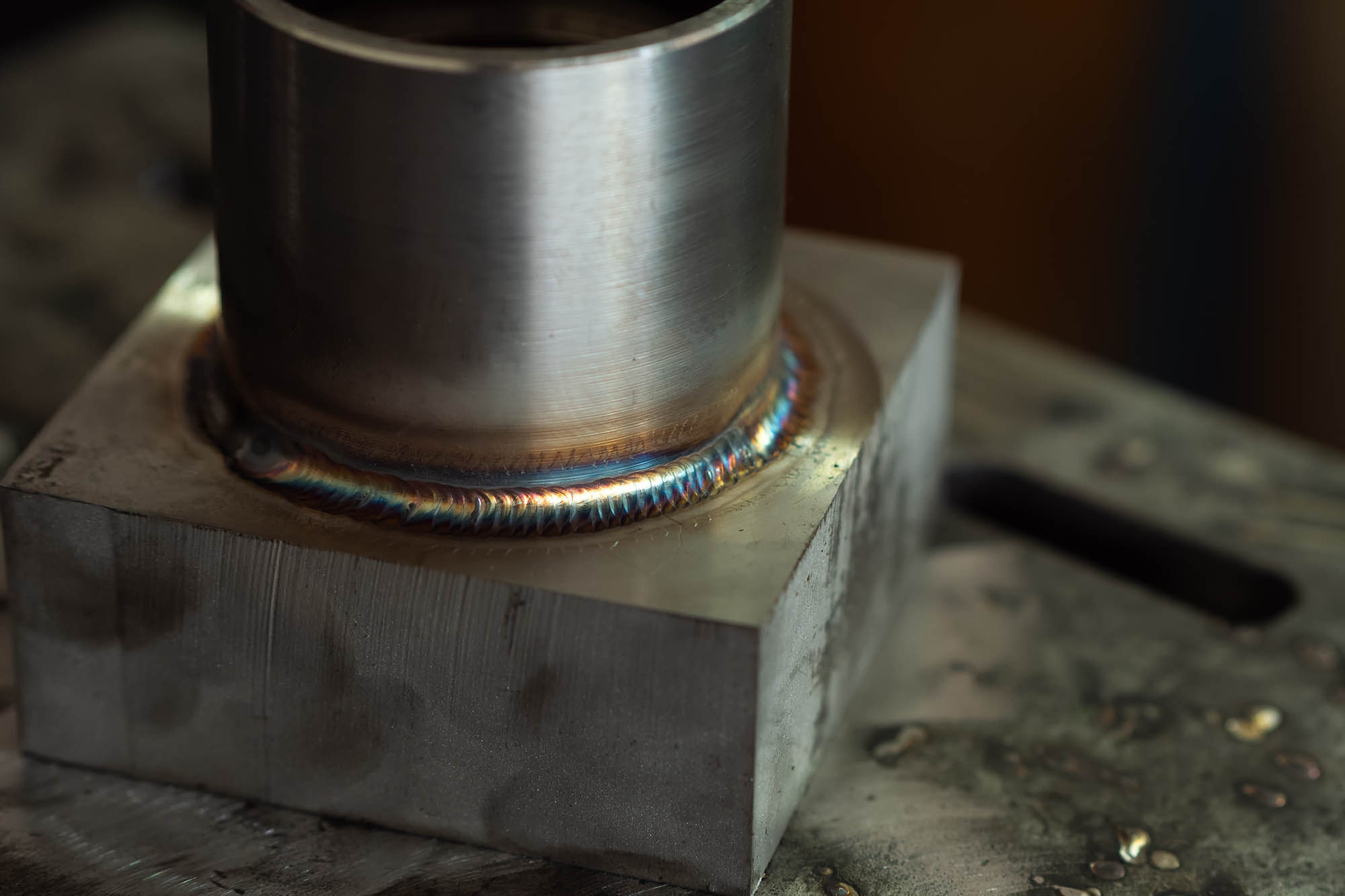
Prevention Techniques Introduction
Provided the destructive impact of porosity on weld top quality, reliable avoidance strategies are crucial to preserving the architectural honesty of bonded joints. Furthermore, selecting the appropriate welding specifications, such as voltage, current, and travel speed, can assist minimize the risk of porosity development. By including these prevention strategies right into welding techniques, the occurrence of porosity can be considerably minimized, leading to stronger and more trustworthy bonded joints.
Significance of Appropriate Protecting
Correct shielding in welding plays a critical role in protecting against atmospheric contamination and guaranteeing the stability of bonded joints. Securing gases, such as argon, helium, or a mixture of both, are frequently made use of to safeguard the weld pool look at here now from responding with aspects airborne like oxygen and nitrogen. When these reactive aspects enter into call with the warm weld pool, they can create porosity, causing weak welds with decreased mechanical homes.
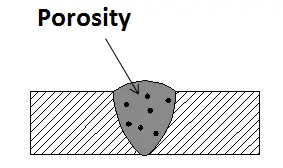
Insufficient protecting can result in various problems like porosity, spatter, and oxidation, compromising the structural integrity of the welded joint. For that reason, sticking to correct shielding practices is necessary to create top quality welds with very little issues and make certain the durability and reliability of the welded useful reference parts (What is Porosity).
Surveillance and Control Approaches
How can welders efficiently check and manage the welding procedure to guarantee optimum outcomes and protect against problems like porosity? By continuously checking these variables, welders can determine variances from the suitable conditions and make instant changes to protect against porosity development.

Additionally, implementing proper training programs for welders is vital for keeping an eye on and controlling the welding process properly. What is Porosity. Enlightening welders on the value of preserving consistent specifications, such as proper gas protecting and travel rate, can aid prevent porosity concerns. Regular analyses and accreditations can likewise make certain that welders are efficient in tracking and managing welding processes
In addition, using automated welding systems can improve monitoring and control abilities. These systems can precisely regulate welding criteria, lowering the possibility of human error and ensuring consistent weld quality. By incorporating sophisticated tracking technologies, training programs, and automated systems, welders can effectively keep an eye on and regulate the welding procedure to lessen porosity use this link problems and achieve high-quality welds.
Conclusion
Report this page